The Ultimate Journey From Manual To Automation
We asked 20 business owners “What does automating your warehouse involve?”. All the replies were slightly different, but all mentioned how an automated warehouse had a greater future perspective, after going through a long and expensive installation with multiple reorganisations. But does it always have to be this way, or have you just been looking at the wrong solutions?
“Automation in intralogistics does not have to go from 0% to 100% all at once. Not every business needs full automation or perhaps not every business is ready to dive in right away. Depending on volume, growth and industry development trends, different businesses can start small and steadily invest in upgrades, i.e. “grow as you go”. Of course, we can advise you on the right path for your organization”, says Jonathon Buckby, Head of Sales at SSI SCHAEFER UK.
Let us start with when and why
Take it from some of the leaders who have already started their journey towards the automated warehouse and hear what pushed them into taking this step.
“In a short time, we have found a solution that provides the conditions to continue our fantastic growth journey and to achieve our set profitability goals. The solution will also offer our logistics employees in Sweden the best working environment!”, - comments Henrik Peitz, COO at Mathem.
“We have seen many shifts to automation within our industry. The productivity rates reached with the automated operations are impossible to get with the manual goods handling,” - shares Mats Tornard, Project Manager of Strategic Supply Chain at Coop.
Knut-Andreas Kran, CEO of ASKO OSLOFJORD AS: “We simply would not be able to keep up with the expected growth in the current location. We also did not want to just build a larger manual warehouse as we see that automation is an investment in the future.”
Every business has a different way of starting automation. Discover projects for market leaders in pharmaceutical and cosmetics, fashion, food retail, е-commerce and many other industries. Do not rush into any decision without thorough research.
How much to automate
Depending on the size of your business, growth, and multiple other factors, there are different degrees of automation to consider.
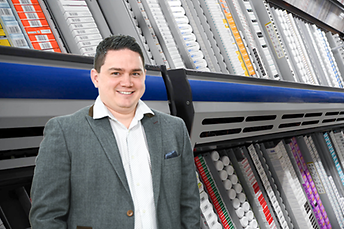
“A smaller step could be introducing a simple technology to reduce the need for manual labour, focusing on an individual process completion time. With this goal in mind, logistics managers may consider installing one or a few pieces of equipment. For example, it may be a conveyor system to connect workstations more easily. Another option, Vertical Lift Module (VLM), works perfectly for small parts storage. The VLM is designed to address the lack of space and improve picking errors”, continues Jonathon.
However, automation does not have to start with equipment. A Warehouse Management System is another choice. It will help with inventory count, order consolidation, more efficient items retrieval, and clearer control of the process overall.
Equipment can be integrated to build a better process design. The above mentioned VLM and conveyor system can be integrated creating exponential benefit. An employee working with a VLM does not have to waste time walking, the conveyor will do it for them, combined with the auto retrieval of VLM. On the flip side, a conveyor system can take up valuable floor space which may not be an option for some areas. In this instance, AGVs may be more flexible and only need a rail or guide on the floor. Moreover, with the intelligent motion tracker, they are safe to operate in manual warehouses with increased pedestrian traffic.
The “big” step to full automation is something that industry leaders selected for their logistics centres – complete automation with minimal involvement of manual process fulfilment. A solution like this could include shuttles for ambient, cold or deep-freeze storage zones, case and piece picking robots, order verifiers and a variety of other technologies.
“With all said, any automation would need to focus around the operations of your business. Technology should only be utilised to improve the ongoing operational requirements. Our intralogistics experts at SSI SCHAEFER can assist with identifying best practice, said Jonathon.
Would you like to speak directly to one of our automation experts? Fill out this short form today.
What to automate
“Knowing the optimal end goal for your businesses is one thing, but it is crucial to break the process into steps as required. Analyse the journey a product takes throughout the logistics centre, from the inbound to outbound, identify how each step can be performed better individually, and as a whole”, suggests Jonathon.
Goods receiving zone
In terms of inventory a simple question pops up: “Is the item’s description and tracking information immediately transferred into the system? Are there scanners for pallet or case labels?”. This is something to consider in terms of clear and well-organised stock, seamless receiving, easier picking and replenishment. Another point to consider is how the receiving zone is equipped. Are items delivered to depalletising or storage buffer manually or by a conveying system?
Handling returns
Having the right approach towards returns is essential, especially for e-commerce. Thousands of smaller orders or items in a B2C environment may be sent back by the customer for a multitude or reasons. This provides one of many pressure points the e-tailers face. Returns is an ever growing percentage based on the growth of e-commerce and unique customer needs. It’s a growing concern but has to be handled differently to standard stock. How these items are handled, stored, identified and treated against future orders all must be considered. Automation can be tailored to meet a range of needs including sortation and future picking.
Picking orders
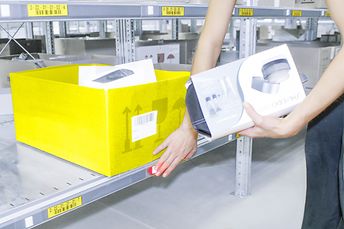
Shipping zone
And now we are at the final phase in the logistics process when goods leave the warehouse to reach a customer, whether that end customer is a business or a person. All the roles here can be handled manually, but with a little help from automation, they can be performed on another level. For example, routes and order details can be automatically printed and applied to packages. The label is scanned, and the data is added accordingly, meaning there will be fewer errors. It will speed up the whole process.
Key takeaways
Logistic centres play a huge role in every business’ supply chain. It can help your business prosper or diminish peak season’s sales results. Definitely not something to overlook. An up-to-date warehouse adds significant value to the customer experience and journey.
“There are dozens of decisions to make when automation is on the horizon. I highlighted just a few crucial points to think over:
Why your logistics centre needs modernisation and what is the end goal?
How far does your business need to go now and are you ready for some advanced technology?
What do the current processes look like and what zones are the bottlenecks?
How can automation facilitate your processes?
Finally, one should always consider future growth by investing in scalable systems. A solution that will accommodate additional areas, more workstations, extra machines, increased sales and orders and extra people following your business’ success path. No two business are the same and neither are their logistical processes. SSI SCHAEFER’s logistics expert can talk you through the best options, whatever your business operations, needs and goals. Do not hesitate to get in touch”, says Jonathon.