Think Safer, Think SSI SCHAEFER: 5 Tips to Ensure Warehouse Safety
Your warehouse is the hub of activity where goods are received, stored, and shipped out to customers. With so many simultaneous activities taking place, it is essential to maintain a safe working environment for everyone involved.
To ensure the continuous running of your operations without downtime, it is important to adhere to the steps discussed in the following blog. By following SSI SCHAEFER's recommended warehouse safety protocols, inspection, and maintenance processes, numerous clients have enjoyed a long-standing record of undisrupted supply chains. SSI SCHAEFER prioritizes protecting our clients, like you and your employees, from costly and avoidable consequences of racks damages during warehouse operation.
Here are 5 practical guidelines for you to check if you're on track to making safety your top priority:
TIP 1: CONDUCT HOLISTIC WAREHOUSE INSPECTIONS AND MAINTENANCE REGULARLY
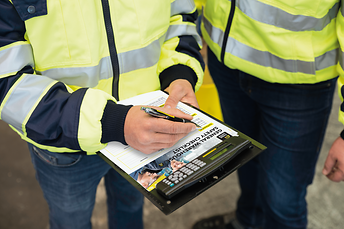
Equipment damage happens. More often than not, these damages aren't easily detectable and often go unnoticed. While high-quality racks and shelving systems are built to last for a long time, they can be damaged during operations due to unsafe user habits. Addressing potential hazards immediately via visual control through all aisles of racks and shelving can prevent any mishaps from happening to the employees working in and around the warehouse. These inspections also reveal areas for improvement whenever any equipment repair, upgrade, or modification is needed. Conduct a holistic rack and shelving inspection at least twice a year, as it is key to fostering a positive safety culture among the operators. Keeping the equipment in good condition reduces the risk of accidents and helps to extend its lifespan.
Are your racks and shelving safety standards in compliance with the European Standards (EN 15635)? Download the checklist or get in touch with us to find out.
TIP 2: DESIGN A PROPER LAYOUT BASED ON MATERIAL FLOW
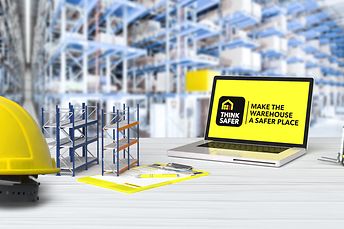
A clean and organized warehouse is critical to maintaining a safe working environment. It not only looks more professional, but it also minimizes the risk of accidents. An organized and well-designed warehouse layout can improve efficiency, productivity, and safety, all thanks to optimized paths to access SKUs quickly and accurately.
Designing a layout that suits your material flow:
Minimizes travel time – Efficiency
Improves order fulfillment rates – Productivity
Ensures compliance with the manufacturers’ racks and shelving safety standards; pallet load capacity, size, and weight of items – Safety
Always take into consideration the frequency of access and the flow of materials through the warehouse. These proactive steps will keep the warehouse clean and neat. Follow the steps below to achieve an organized warehouse:
Practice good storage habits and maintain clear walkways and unobstructed emergency exits
Clean up all clutter and spills on walkways and aisles immediately to prevent slips and falls
Ensure proper lighting to help employees see potential hazards and navigate the workspace and reduce the risk caused by inadequate visibility
If you need help determining which equipment to use or have concerns about the safety of your current equipment, it's best to contact the manufacturer to redesign the layout for you. We at SSI SCHAEFER can help you add, modify, or retrofit your storage systems to adjust the material movement speed and ensure your equipment is appropriate for the job.
TIP 3: IMPLEMENT AUTOMATION SYSTEMS
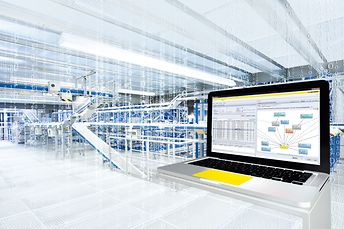
Automating a warehouse can significantly increase safety for employees in several ways. Holistic automation involves assessing your warehouse processes and identifying areas that can be automated. This means partially or completely removing workers from dangerous work procedures and potentially reducing manual handling of goods.
Reduce manual handling: Using conveyor belts, Automated Storage and Retrieval Systems (ASRS), and Autonomous Guided Vehicles (AGVs) to move and handle goods within the warehouse can reduce the need for manual handling of heavy or bulky items, minimizing the risk of musculoskeletal injuries.
From manual to semi-automated storage systems handling, use the Mobile Racking Systems (MRS). The flexible mobile carriages are equipped with emergency stop switches, photoelectric access barriers, manual release systems, proximity sensors, and photoelectric safety barriers. Watch how the Mobile Racking Systems (MRS) works.
SSI SCHAEFER automated systems are programmed to follow safety protocols strictly. The machinery or equipment alerts workers of potential danger, stopping when a safety sensor is triggered or only operating when a specific set of conditions is met (Note: Read on to find out: “Machinery vs. Equipment”). It’s important to carefully evaluate your needs and work with experienced professionals to design and implement the right automated solutions to prevent fatalities and injuries.
TIP 4: USE THE RIGHT MACHINERY AND EQUIPMENT SAFELY
When operated correctly with proper safety measures, warehouse machinery and equipment can ensure a safer workplace and reduce human error. Here is a quick overview of “Machinery vs. Equipment”:
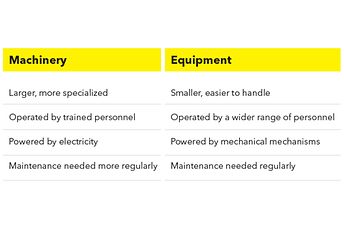
Using appropriate material handling equipment such as forklifts and hiring certified operators that are properly trained and certified can avoid accidents. Choosing the right forklift for the job and properly storing items according to weight capacity can also help prevent collapses and product damage. When determining the appropriate storage location for goods, two primary factors to consider are the dimensions of the goods and the weight capacity of the pallet. This ensures that the pallet can effectively support the weight of the goods without any safety issues.
TIP 5: ENFORCING SAFETY PROTOCOLS
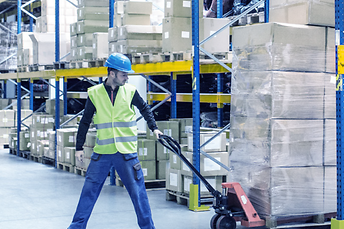
Final tip! Offer your employees regular refresher courses and ongoing training to reinforce safe habits and prevent accidents. Employees, especially new hires, should be trained on proper lifting techniques, using the right equipment, and life-saving emergency procedures. They should also be trained on the potential hazards in the warehouse and know how to avoid them. By playing the right role to equip them with the latest safety procedures and practices, you are creating a positive work environment that can boost employee morale and reduce the risk of accidents and injuries. Upon your due diligence in providing the right training, contact our Customer Service & Support (CSS) department – whereby our scope of services includes all services related to the maintenance of your system throughout its life cycle – 365 days a year. Sign up for a free consultation with us now.
The Way Forward
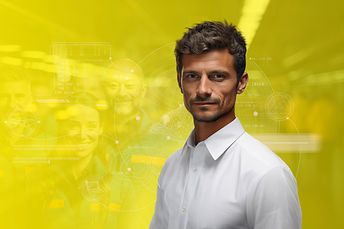
In conclusion, creating a safe warehouse environment is a continuous process that requires ongoing attention and effort. Prioritizing training, implementing safety protocols, keeping the warehouse clean and organized, ensuring proper lighting, regularly inspecting equipment, addressing near misses and incidents, and encouraging employee involvement can help ensure the safety of both employees and inventory. As a responsible company, you have the duty to ensure that your operations are conducted in a safe and responsible manner. Have more questions related to warehouse safety? Contact us for a free consultation now. Think Safer, Think SSI SCHAEFER.