Tiefkühllager: So lösen Sie die drei Hauptprobleme
Die aktuelle Krisen haben in vielen Bereichen eine Wende herbeigeführt, da sie bekannte Probleme aufzeigen, wie beispielsweise die fehlende Digitalisierung von Prozessen oder den Fachkräftemangel, und noch einmal verstärken. So mussten diese Herausforderungen in kürzester Zeit gelöst werden, um wettbewerbsfähig zu bleiben und das Fortbestehen des Unternehmens zu sichern. Auch die Tiefkühllogistik ist einer der Bereiche, wo neue Lösungen gefunden werden müssen
Die Betreiber von Tiefkühlanlagen sind daher gezwungen, nach neuen Lösungen zu suchen. Weitermachen wie bisher ist keine Option. Um Energiekosten zu senken, dem Fachkräftemangel entgegenzutreten und den Platzbedarf durch das eigene Wachstum möglichst effizient zu gestalten, sollten Unternehmen sich mit der Teil- oder Vollautomatisierung ihrer Lager auseinandersetzen. Unabhängig davon, ob es um die Erweiterung bestehender Anlagen geht oder den Bau eines neuen Distributionszentrums handelt. SSI SCHÄFER bietet zukunftsorientierte Lösungen für die Kühllager, die auf den Kunden zugeschnitten sind.
In unserem Best Practice Guide zum Thema Tiefkühllager finden Sie alle relevanten Strategien für eine zukunftsfähige Tiefkühllogistik:
Automatisierung als Problemlöser für Tiefkühllager
Automatisierung bietet eine erprobte und zukunftsfähige Möglichkeit, die drei Hauptprobleme der Tiefkühllogistik zu lösen
Fachkräftemangel
Platzmangel
Hohe Energiekosten
Manuelle Tätigkeiten bei der Tiefkühllagerung minimieren
Der Mangel an qualifizierten Arbeitskräften auf dem Markt ist eines der häufigsten Probleme beim Betreiben von Tiefkühlanlagen. Die Arbeit in einem Lager ist oft mit schwerem Heben, sich wiederholenden Aufgaben und sogar mit Arbeiten in gefährlicher Höhe verbunden. Der Fachkräftemangel ist in Tiefkühllagern besonders groß, da die Arbeitsbedingungen dort für die Mitarbeiter:innen im Allgemeinen weniger attraktiv sind, denn sie müssen einen Teil ihres Arbeitstages bei sehr niedrigen Temperaturen verbringen. Das Arbeiten im Tiefkühllager ist zudem mit vielen Vorschriften verbunden, was eine genaue Planung voraussetzt. Dadurch wird Flexibilität eingebüßt.
Dies wird noch deutlicher, wenn wir manuelle Tätigkeiten betrachten. So verbringen beispielsweise Mitarbeiter:innen, die für die Kommissionierung von Ladungsträgern zuständig sind und Gabelstaplerfahrer einen großen Teil ihres Arbeitstages in den Tiefkühlbereichen.
Teil- oder Vollautomatisierung ist das richtige Mittel, um die oben genannten Herausforderungen zu bewältigen. Automatisierte Lösungen verringern den Personalbedarf in Tiefkühllagern, sind aber in der Regel nicht darauf ausgelegt, vorhandene Mitarbeiter:innen zu ersetzen.
Eine der möglichen Lösungen kann hier eine Reorganisation des Arbeitsprozesses in Verbindung mit einem gewissen Grad an Automatisierung sein. So können Fördertechnik, Shuttle-Lager oder Regalmaschinen für das Handling, die Tiefküllagerung sowie Kommissionierung von Behältern und Paletten sowie den anschließenden Transport der Ladungsträger zu den Arbeitsplätzen eingesetzt werden. Auf diese Weise sind die Mitarbeiter:innen an der Auftragszusammenstellung beteiligt, allerdings von einem ergonomischen Ware-zur-Person-Arbeitsplatz aus und in einer Umgebung, die über dem Gefrierpunkt liegt. Dadurch werden die Arbeitsbedingungen für potenzielle Mitarbeiter:innen attraktiver.
Hochverdichtete Tiefkühllager
Das Thema Platzmangel ist einer der drei Hauptgründe für Unternehmen der Tiefkühllogistik, bestehende Anlagen zu erweitern oder einen Intralogistik-Experten zu beauftragen, der das Layout der aktuellen Immobilie überprüft, neue Lösungen in das bestehende System integriert oder es auf Halb- oder Vollautomatisierung umstellt.
Im Tiefkühllager ist einfaches und schnelles Handling erforderlich. Wenn die Teilautomatisierung im Moment die bessere Option ist, könnten Verschieberegale eine Lösung sein. Diese optimieren den Platzbedarf und bieten eine hohe Lagerkapazität. Da Raum bei Tiefkühllagern teurer ist, sollte eine Technologie genutzt werden, die zusätzlichen Lagerraum mit minimaler Gangfläche schafft.
Die Raumoptimierung kann auch mit einer vollautomatisierten Lösung wie dem Hochregallager (HRL) gelöst werden. Auf diese Weise wird der gesamte vertikale Raum bei der Tiefkühllagerung optimal ausgenutzt. Das HRL ist ein vollautomatisches Regalsystem in Kombination mit Regalbediengeräten (RBG), welches eine unglaublich dichte Lagerung auf kleinem Raum ermöglicht. Dies ist bei Tiefkühllagern besonders wichtig, da jeder Kubikmeter innerhalb des Lagers auf die spezifischen Bedingungen eingestellt werden muss, auch wenn er das Produkt nicht lagert.
Oft hilft eine Automatisierungslösung, mehr als ein Problem der Kühl- und Tiefkühllagerung zu lösen. Zum Beispiel benötigt ein HRL aufgrund der dichten Bauweise nicht nur weniger Platz, sondern auch weniger Energie.
Optimierung des Energieeinsatzes in der Tiefkühllogistik
Die Energiekosten machen einen der größten Anteile am Budget bei Tiefkühllagern aus. Bei der manuellen Lagerung müssen die Regale in der Breite angepasst werden, damit sowohl Menschen als auch Gabelstapler die Kommissionierung bei tieferen Temperaturen durchführen können. Das bedeutet mehr Platz zum Kühlen und Beleuchten der Kühl- und Tiefkühlanlagen, wodurch die Kosten steigen. Die Energiekosten können durch Automatisierung optimiert werden, um Unternehmen bei dieser Aufgabe zu unterstützen.
Für die Teilautomatisierung können beispielsweise Kanallager eine großartige Lösung sein. Diese bieten eine kompakte Lagerlösung innerhalb eines definierten Bereichs. Mehrere Lagerplätze werden nacheinander in sogenannten Kanälen angeordnet. Ein Kanallager ist besonders verdichtet und nutzt den Raum viel effizienter als herkömmliche Regale.
Vollautomatische Shuttle-Systeme und Paletten-RBG werden mit Blick auf Energieeinsparungen gebaut. Einige der Lösungen können sogar im Dunkeln oder mit weniger Beleuchtung arbeiten, um weitere nachhaltige Vorteile zu erzielen. Dies ist etwas, das mit manuellen Arbeitsprozessen nicht erreicht werden kann.
Maßgeschneiderte Lösungen als Erfolgsfaktor für die Tiefkühllogistik
Die genannten Lösungen sind Beispiele dafür, wie Unternehmen die Herausforderungen der Tiefkühllagerung bewältigen können. Dabei sollte jede Lösung an das bestehende Geschäftsmodell und die aktuellen Bedürfnisse des Kunden angepasst werden.
Das perfekte System wird auf der Grundlage einer Datenanalyse, der richtigen Lösungskonzeption für die verfügbare Fläche des Kunden und seine zukünftigen Wachstumsziele entwickelt. Es kann eine Herausforderung sein, eine Reorganisation nur mit internen Ressourcen durchzuführen, und das ist der Zeitpunkt, an dem ein Intralogistik-Experte unterstützen kann. SSI SCHÄFER bietet jedem Unternehmen, ob klein oder groß, maßgeschneiderte Lösungen für Tiefkühllager, um die gesetzten Ziele zu erreichen.
Das Expertenteam von SSI SCHÄFER verfügt über jahrelange Erfahrung mit einigen der größten Tiefkühlanlagen der Welt, aber auch mit vielen kleinen und mittelgroßen realisierten Lösungen. Jede Lösung wird auf die spezifischen Geschäftsanforderungen des Kunden zugeschnitten.
Was unsere Kunden sagen
Wir hätten die Prozesse so belassen können, wie sie seit 35 Jahren sind - mit vollständig manuellen Abläufen. Wir waren uns bewusst, dass wir so nicht mehr konkurrenzfähig sind. Die einzige Möglichkeit, wettbewerbsfähig zu bleiben, ist der Einsatz von Technologien.
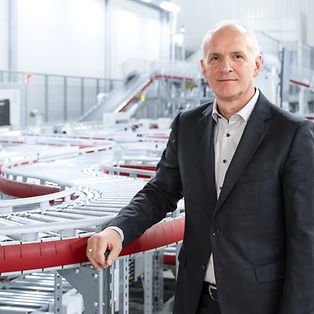
Als erster Anbieter von vollautomatischen Kühllösungen auf den Philippinen ist ORCA das erste und einzige Unternehmen, das in diesem Umfang in die Lebensmittelinfrastruktur investiert. Als Vertriebsleiterin konnte ich beobachten, dass sich Kunden aufgrund unserer Automatisierungspläne von unserer Marke angesprochen fühlen. Wir haben aus erster Hand erfahren, wie der Markt den Wert von Innovationen wahrnimmt und wertschätzt.

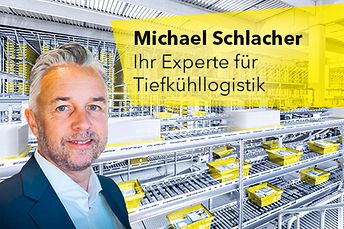
Über den Autor:
Nach langjähriger Erfahrung in Intralogistikunternehmen, unter anderem in leitenden Funktionen in den Bereichen Projektmanagement und Sales, kam Michael Schlacher im Jahr 2021 zu SSI SCHÄFER und ist als Senior Sales Manager für das Business Development verantwortlich.