VOG Expands Warehouse Capacity with Intralogistics Systems by SSI SCHAEFER
First-time investment by VOG AG in a fully automated pallet high bay warehouse
More efficient, quicker, and safer fulfillment processes in wholesale logistics
Ideal solution for combating labor shortages and rising energy costs
Parallel expansion of conventional warehouse system capacity by SSI SCHAEFER
Facing a crisis in the supply of sugar during the First World War, 21 Upper Austrian food wholesalers decided in 1916 to found VOG AG in Linz as a buying association. Further expansion has been and continues to be driven by the fact that the food industry and its regulation is constantly changing. A willingness to evolve and adapt to new market and customer requirements has therefore been an important factor in the company’s success. VOG is respected for its quality control, product safety, and variety, both for own brand and private label goods as well as items in the non-food sector.
Objective: Performance and efficiency in harmony
As a service company for the retail sector, the traditional Austrian company operates a broad logistical infrastructure network with 12 subsidiaries. Central distribution warehouses for customers throughout central Europe can be found in countries such as Austria, Poland, Czech Republic, and Hungary. All logistics activities throughout the entire group are coordinated by the in-house service provider VOGTRANS Speditions- und Verpackungsgesellschaft mbH. “Having full transparency over all items in stock is becoming increasingly important as the requirements for product traceability continue to grow,” says Matthias Ritzberger, CEO and board member of VOG. Rising operating costs are also forcing a rethink in how resources are used, while stock security – especially during seasonal peaks – is another critical aspect. “In the face of these challenges and in light of the impressive solution concept from SSI SCHAEFER, which was superior to those from other suppliers, we decided in early 2021 to set a course for the future together with SSI SCHAEFER,” explains Matthias Ritzberger.
Impressive needs-based, holistic solution concept
The solution proposed by SSI SCHAEFER included the construction of a new manual warehouse as well as a fully automated pallet high bay warehouse. Both were to be incorporated into and linked up with the existing infrastructure at VOG’s site in Linz as effectively as possible. “The high bay warehouse is our first-ever fully automated system,” says Matthias Ritzberger. The goal was for goods to be staged more quickly and with a minimized error rate, while at the same time having greater resource independence. Other objectives included optimized processes and a higher storage density. “The concept presented by SSI SCHAEFER impressed right from the start,” adds Matthias Ritzberger. “The facts were laid out clearly and the quoted solution was tailored exactly to our needs.”
Flexibility for today and tomorrow guaranteed
“In order to ensure continuous and efficient workflows while also establishing the right basis for future growth, a cautious but steady rollout of automated solutions is advisable,” says Jürgen Ringelmann, project manager at SSI SCHAEFER. “Companies can follow VOG’s example and begin by automating just a few areas to begin with, allowing them to gain initial experiences with the technology before defining their own priorities for the future.” After a construction and installation phase of just two years, the new systems were commissioned on time and as planned at the start of 2023. The pre-zone of the pallet high bay warehouse is connected to an existing hall by a newly integrated, bidirectional conveying system via which goods can be flexibly carried into and out of the warehouse. It is also connected to a dispatch building. The high bay warehouse is primarily used for storing rapeseed oil carrying the “Rapso” own brand label, as well as canned food and wine produced by VOG itself. It has capacity for up to 11,000 pallets in double-deep storage thanks to four energy-efficient SSI Exyz storage-retrieval machines by SSI SCHAEFER. “VOG intentionally opted for an in-house design,” says Jürgen Ringelmann. “This allows the customer to keep all their options open regarding how they will potentially want to use the system in 20 or 30 years’ time.” An extra 11,000 storage locations for pallets have been created in a newly built manual warehouse containing 15 aisles. The rack lines needed were also supplied and installed by SSI SCHAEFER.
WAMAS – Performance targets greatly exceeded with software support
Another first for VOG came in the form of the logistics software WAMAS by SSI SCHAEFER. The WAMAS MFS material flow system continuously controls and optimizes processes in the fully automated pallet high bay warehouse from goods-in to goods-out. Real-time comparison between the WAMAS WCS (warehouse control system) and MFS ensures that orders are always assigned on the basis of where capacity is available in the conveying system and picking areas, allowing last-minute priority orders and peak situations to be effectively managed. “The performance of automated systems is always dependent on the underlying software,” explains Jürgen Ringelmann. With VOG AG in particular, the contractually agreed benchmarks could even be exceeded thanks to the WAMAS WCS. Depending on the order structure, the system is able to handle up to 180 pallets per hour.
Preventive maintenance and short response times in service cases guarantee optimal system protection and continuous performance
Maximum availability over the entire lifetime of the system was a priority of utmost importance for VOG. Thanks to preventive maintenance performed by SSI SCHAEFER service technicians, the system can be operated at a constant high level of performance. If a fault does nevertheless occur, quick and efficient remote support is provided via the hotline. Alternatively assistance can be sought through the SSI Augmented Support solution. SSI Augmented Support is a mobile video communication system through which events can be reported in real time, allowing the technician at VOG AG to begin identifying the problem immediately. If the fault cannot be rectified remotely, trained and certified SSI SCHAEFER service technicians assist on-site to resolve the issue quickly and thus ensure smooth operation of the system.
Greater performance and lower costs achieved as planned
“Our experiences with the automated system in Linz have been overwhelmingly positive ever since it went live,” emphasizes Matthias Ritzberger from VOG. “The system does not have to be run at full capacity round the clock, which saves energy. But thanks to the scalable buffering function created by SSI SCHAEFER, it can be ramped up again in no time to significantly increase its technical performance. This has the advantage that the system is not only capable of handling seasonal peaks, but has the capacity to accommodate future growth as well.” VOG is also operating on a sound basis when it comes to stock management thanks to the software-based continuous inventory, which ensures that replenishment can be ordered in good time. At the same time, it is apparent that the high bay warehouse as a self-contained, high-density storage system can be operated much more energy-efficiently in the medium to long-term than manual warehouse areas with people and forklifts. Part of this is down to the SSI Exyz storage-retrieval machines, which save energy during the lifting movement thanks to a counterweight integrated into the mast. If further investments into logistics systems are being considered at a later time in the VOG Group, the experiences gained with the automated system installed by SSI SCHAEFER will certainly influence the final decision.
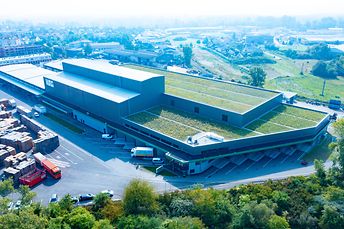
VOG AG, an Austrian company rich in tradition, operates a large logistical infrastructure network with 12 subsidiaries.
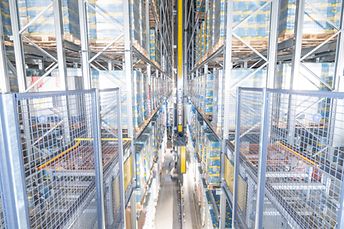
The high bay warehouse has capacity for up to 11,000 pallets in double-deep storage thanks to four energy-efficient SSI Exyz storage-retrieval machines by SSI SCHAEFER.
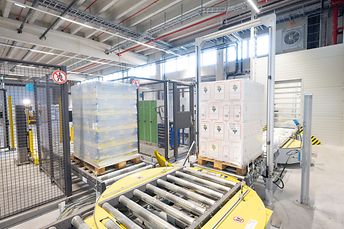
The pre-zone of the pallet high bay warehouse is connected to an existing hall by a newly integrated, bidirectional conveying system via which goods can be flexibly carried into and out of the warehouse.
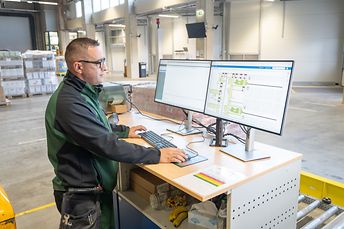
The WAMAS logistics software continuously controls and optimizes processes in the fully automated pallet high bay warehouse from goods-in to goods-out.
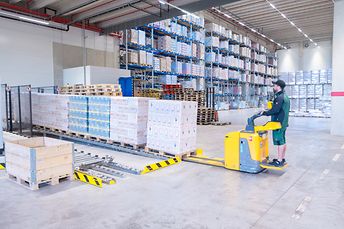
Depending on the order structure, the system is able to handle up to 180 pallets per hour.
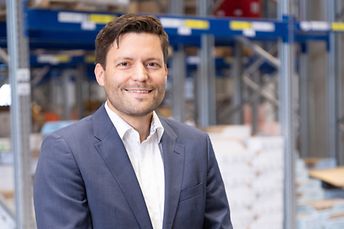
Matthias Ritzberger, CEO and board member of VOG.