SSI SCHAEFER Implements High-Performance Logistics Center for Carhartt WIP
High-Performance Fashion Logistics for Efficient Omnichannel Management
SSI SCHAEFER served as the general contractor to equip a new logistics facility in Weil am Rhein with a state-of-the-art systems technology for Work in Progress Textilhandels GmbH (Carhartt WIP). SSI SCHAEFER’s powerful intralogistics solution seamlessly connects the existing system with the new one. It ensures process efficiency and optimizes order processing in the respective distribution channels – wholesale, e-commerce and retail. The warehouse capacity has also been expanded to accommodate the steady growth in the e-commerce business. The fully scalable installed intralogistics solution includes an SSI Cuby shuttle system, a compact carton and bin conveyor system, various handling systems and sequence towers.
The “Carhartt WIP” premium streetwear brand is known for casual, timeless styles and durable quality. The company behind the label is Work in Progress Textilhandels GmbH, which manufactures and distributes Carhartt products outside the USA. The new reality of e-commerce-driven shopping presents even a successful fashion supplier like Carhartt WIP with the challenge of ensuring efficient processing of online orders and maximum availability of merchandise as the product range grows. The process needs to manage daily and seasonal peaks flexibly and quickly process returns. With “Shop-Friendly-Delivery”, merchandise must be supplied reliably and quickly to the brick-and-mortar retailers. They receive the goods from Carhartt WIP pre-sorted and optimized for the specific store.
Linking New and Existing Structures Intelligently
Carhartt WIP supplies its own stores and outlets worldwide (B2B); at the same time, orders are also increasing from end customers (B2C) through its own online store and other digital platforms. As a result, Carhartt WIP experienced a shortage of warehouse capacity. Carhartt WIP needed a solution to minimize the rising complexity of omnichannel management. In addition, integrating the dynamically growing e-commerce part of the B2C segment into processes without fundamentally modifying tried-and-tested B2B business procedures was a major challenge. This challenge had to be met on the software side; however, from a technical point of view, it also meant seamlessly connecting the existing system to a new, expanded intralogistics system in such a way as to allow continued use of existing systems. Furthermore, given Carhartt WIP’s expected growth figures, it was essential, even at this stage, for SSI SCHAEFER to plan for optional expansion scenarios in order to allow their seamless implementation in the future during ongoing operations.
Reliable, Proven Collaboration
A logistics project in Weil am Rhein first brought Carhartt WIP and SSI SCHAEFER together many years ago. In that project, the intralogistics specialist optimized and automated the processes in the first logistics facility, with a focus on the automated small parts warehouse (ASPW). “We commit to SSI SCHAEFER based on a long-standing collaboration with trust and a high degree of reliability,” says Wolfgang Heldt, Head of Logistics at Carhartt WIP. Given the increasing success of e-commerce, the expansion of the logistics center was the next logical step: “Customers expect a certain level of service, and online vendors need to maintain that level 24 hours a day, 365 days a year. Furthermore, for Carhartt WIP, this performance must reflect our premium brand’s reputation,” emphasizes Wolfgang Heldt. In particular, the expansion project focused on maximum flexibility and efficiency, modularity, and built-in buffers for future growth. These features are essential for an adequate response to current and future challenges – from a business perspective as well.
Perfectly Coupled Service Modules for Greater Efficiency
In the extension building with around 4,000 m² of floor space, SSI SCHAEFER installed a fully automated, space-optimized shuttle storage system in which 110 SSI Cuby single-level shuttles handle storage and retrieval. Around 35,000 container and carton storage locations with double-deep storage, distributed over five aisles, were created. “The SSI Cuby shuttle system is very powerful – the performance we get, 22 shuttles per aisle, is remarkable and has led to a reduction in order throughput times,” says Wolfgang Heldt, adding: “The shuttle storage system allows us to efficiently meet the needs of the B2C business, where low order quantities are the norm.” Depending on the order structure, Carhartt WIP can now handle up to 100,000 picks in one day. Lifts, which ensure high throughput, as well as the infeed and take-away conveyor systems, including a high-speed loop, are connected to the shuttle storage system. The ten sequence towers, each with 2 × 22 transfer locations, serve to sequence the source cartons and continuously supply the ten picking stations, which are equipped with put-to-light displays. “These towers efficiently buffer and sequence cartons retrieved from the shuttle storage system to ensure that they’re always fed to the picking stations in the correct sequence,” explains Johannes Zach, Vice President Market Sector Fashion at SSI SCHAEFER. “This increases process reliability while boosting performance.”
The workstations in the different areas, such as incoming goods, order picking, new incoming returns and packaging, are connected through the conveyor system. In addition, the eight new B2C packaging workstations and the six special handling workstations for value-added services, such as prepricing and customer-specific carton or pallet loading, are also integrated. These processes are supported by various handling systems, e.g., automatic carton openers and erectors, scanners, automatic sealing machines and label applicators. The conveyor system also connects the eight-aisle ASPW, to which SSI SCHAEFER has added two further aisles. This made it possible to create completely new material flow structures and link them to the processes in the B2B area, which were mostly retained, in order to efficiently handle the seven defined order scenarios. These result from the different composition of the items, which can come from up to three warehouse areas: the existing ASPW, the block storage for non-conveyable items and the new shuttle storage system. “Due to the complexity of the system elements and processes, we divided the commissioning in two phases,” adds Udo Peintner, project manager at SSI SCHAEFER. “Phase one, which was completed in January 2020, involved the ASPW expansion and retrofitting the existing system, incoming goods and switching the existing software to WAMAS®. This was followed in September 2020 by the go-live of the SSI Cuby system, the sequence tower and the connection of the existing system to the new shuttle storage system through the conveyor system.” As a result, the overall system was able to deliver the required performance in time for “Black Friday” and “Cyber Monday” – promotional discount events popular with consumers.
During project implementation, SSI SCHAEFER delivered the individual pieces, such as steel construction, the conveyor system, the shuttle system, and software as a complete package. This was an advantage since the reduction in the interfaces involved benefited Carhartt WIP through time-optimized project execution.
WAMAS® – the Pulse Generator for the Overall System
The intelligent WAMAS® Warehouse Control System (WCS) connects people and service modules and harmonizes processes in warehouses – a crucial contribution to making order processing efficient. The WAMAS WCS controls automated processes within the warehouse in real time and ensures a constant material flow. Should conditions change, the system reprioritizes operations so that fulfillment performance meets current needs and is accelerated. It also uses the SCADA system visualization of WAMAS Lighthouse, which provides a realistic representation of the entire system and lets you derive precise insights into the smallest details on different levels. This ensures countermeasures are initiated quickly if critical operating states are imminent, ensuring maximum availability.
Maximum Throughput for Constant Availability of Goods
“We’ve been bowled over by our success in the past two to three years,” reports Wolfgang Heldt. “As a result of the pandemic, the proportion of online orders has increased by leaps and bounds. The shuttle storage system puts us in a good position, and we plan to work with SSI SCHAEFER to expand it in the near future with three additional aisles, which will give us around 125,000 available item storage locations at the Weil am Rhein site.” Thanks to the WAMAS® logistics software, the dynamic, fully scalable warehouse logistics solution from SSI SCHAEFER provides the perfect interplay among the new and existing storage systems, the sequence towers, and the new and existing picking workstations. This ensures that Carhartt WIP can process a wide variety of order scenarios in the best way possible.
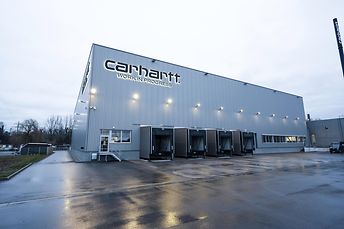