Peterstaler Mineralquellen Invests in Fully Automated Channel Storage System from SSI SCHAEFER
The long-established and successful mineral water producer Peterstaler Mineralquellen, based in Germany’s Black Forest, is building a new logistics hall at its Bad Rippoldsau site. To ensure efficient storage and dispatch of goods produced at the facility, SSI SCHAEFER is implementing a fully integrated intralogistics solution. Commissioning is scheduled for the end of 2025.
With more than 200 million bottles sold last year, Peterstaler Mineralquellen achieved a new sales record. The company’s impressive growth is largely driven by the success of its "Black Forest" brand, which has quickly climbed to become the third most popular still mineral water in Germany.
To keep pace with rising demand, Peterstaler is reactivating its production site in Bad Rippoldsau. In January 2025, installation of a new filling line with a capacity of 35,000 PET bottles per hour began there. To support this expansion, SSI SCHAEFER is delivering a fully automated channel storage system that will buffer goods directly from production. In addition to storage, the retrieval and loading processes will also be fully automated.
Maximized capacity in a compact footprint
For structural reasons, the height of the warehouse is limited to 9 meters. To make the most of the available space, SSI SCHAEFER designed a compact channel storage solution. On just 1,400 square meters of floor space, more than 2,200 pallet storage locations will be created across two opposing blocks within the logistics hall. Between these blocks runs a central conveyor system, which delivers pallets directly from production.
Storage and retrieval in both channel systems will be managed by the high-performance SSI Lift & Run shuttle system. Engineered for facilities with low ceiling heights, the solution provides excellent throughput. The autonomous load handling device SSI Orbiter LHD (Load Handling Device) is used to handle the pallets in the storage channels. The channel vehicle serves all storage locations, ensuring highly dynamic processes. The system is designed to handle more than 60 double cycles per hour. Pallets are automatically transported from storage to outbound loading docks via the central conveying system, and final truck loading is fully automated by an additional integrated system.
A key element of the solution is the seamless integration of WAMAS Material Flow System (MFS) into Peterstaler’s existing IT infrastructure, including ERP and WMS platforms. The WAMAS Control Center serves as a central information platform that visualizes and monitors all intralogistics processes in the warehouse and provides relevant key performance indicators. This close IT integration creates the conditions for a stable material flow with high throughput and enables Peterstaler to use the expanded capacities of the Bad Rippoldsau site efficiently in line with market requirements.
A fully integrated turnkey solution
Implementation of the channel storage system will begin in early summer 2025, with go-live expected by year’s end. The short project timeline is made possible by SSI SCHAEFER’s comprehensive portfolio of products and services – a decisive factor in Peterstaler’s vendor selection.
With SSI SCHAEFER, we’ve found a partner who truly understands our needs for efficiency, flexibility, and long-term viability. Their fully automated intralogistics solution puts us in an excellent position to meet growing customer demand moving forward.
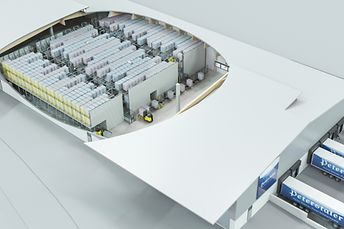
Compact channel storage with SSI Lift & Run shuttle system: Over 2,200 pallet storage locations on 1,400 m² at a height of 9 m.
Logistics Center Bad Peterstal: Founded in 1926, Peterstaler Mineralquellen is a traditional company from the Black Forest offering a wide range of mineral waters.
© Peterstaler Mineralquellen GmbH