Liebherr is constructing a new logistics centre in Tupelo, Mississippi – SSI SCHAEFER is responsible for delivering the intralogistics solution
Liebherr will be constructing a modern logistics center in Tupelo, Mississippi, while SSI SCHAEFER will be responsible for the planning and delivery of the customised intralogistics solution.
The new facility is designed to boost logistics capabilities and strengthen the Liebherr Group’s presence in the American market.
As system integrator, SSI SCHAEFER is delivering a fully automated intralogistics solution featuring high-bay and shuttle warehouses, conveyor systems, and SAP Extended Warehouse Management for highly efficient and transparent warehouse operations.
The Liebherr Group is a family-run technology company with a highly diversified product portfolio spanning 13 product segments. The company is one of the largest manufacturers of construction equipment in the world and a provider of high-quality, user-oriented products and services in a wide range of other areas. The new logistics center, Liebherr Logistics USA, Co. in Tupelo is operated by Liebherr-Logistics GmbH, the group’s in-house logistics provider, and will handle spare parts logistics for several production companies. With over 430 employees, Liebherr-Logistics GmbH currently supplies more than 70 Liebherr sales and service locations worldwide, supporting over 20 product lines. Operating out of Oberopfingen, Germany, since 2015, the company expanded its European footprint in 2023 with a second warehouse in Born, Netherlands. The Tupelo facility marks a major milestone in Liebherr-Logistics GmbH’s expansion into the Americas.
The new logistics hub in Tupelo will handle warehousing, distribution, pre-assembly, repackaging, customs clearance, and export operations. It will serve multiple business units, including earthmoving equipment, cranes, concrete technology, and components - with more to follow. “This new facility allows us to offer faster, more efficient service to our customers and reinforces our position as an industry leader,” says Jörg Ströbele, Managing Director of Liebherr-Logistics GmbH. Designed with cutting-edge technology, sustainability, and scalability in mind, the new site underscores Liebherr’s commitment to future-ready infrastructure. Long-time partner SSI SCHAEFER was chosen due to its trusted track record and ability to deliver the entire project seamlessly from a single source.
SSI SCHAEFER: A Trusted Intralogistics Partner
As system integrator, SSI SCHAEFER will manage the complete delivery of warehouse and conveyor technology and oversee all involved intralogistics trades. At the heart of the system is a seven-aisle high-bay warehouse with over 39,700 pallet positions. Constructed as a rack supported high-bay warehouse that eliminates the need for a separate building, optimizing space and resource efficiency. The SSI Exyz Automated Storage and Retrieval System (ASRS) ensures efficient and sustainable high-density storage of pallets
The facility will also include an eight-aisle shuttle ASRS system equipped with over 450 SSI Flexi Shuttles, offering around 170,000 storage locations for totes. Thanks to SSI SCHAEFER’s patented 3D-MATRIX Solution®, the system will enable optimal sequencing for small parts picking. Additional manual warehouse areas will include over 9,500 locations in PR 600 pallet racks, 690 locations in cantilever racks, and more than 1,100 storage positions for oil and hazardous materials. Picking will take place at five pallet workstations and eight tote workstations, with additional areas for repacking and packaging in development. Conveyors for pallets, totes, and cartons, along with an electric floor track system, will seamlessly connect the facility’s core components.
Warehouse management is handled directly through SAP Extended Warehouse Management (SAP EWM), providing comprehensive capabilities for managing and controlling the entire logistics solution. Implementation is carried out by SWAN GmbH, a member of the SSI SCHAEFER Group. In addition to the functionalities for warehouse management, SAP EWM is supplemented by the integrated Material Flow System (MFS) and linked directly to the automatic warehouse control systems. In this way, the software specialists also ensure the material flow processes of the complex intralogistics system at the highest level.
Future scalability is already built into the concept, with the system designed to double its throughput capacity. This allows Liebherr to expand performance even further as needed.
Looking ahead to the go-live, Jörg Ströbele remarks: “We’ve had a strong, long-standing partnership with SSI SCHAEFER, and we’re confident that the new warehouse will perfectly align with our operational needs. The solution enables us to continue providing fast service and reliable spare parts deliveries – ensuring we’re well-prepared for the future.”
For the Liebherr Group, the new logistics facility in Tupelo represents a strategic investment in its global supply chain. Installation is set to begin in September 2025, with operations scheduled to start in 2027.
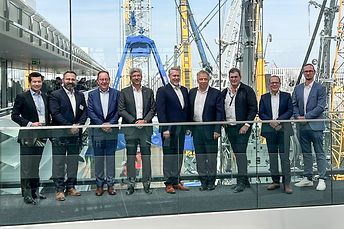
© Liebherr
Liebherr and SSI SCHAEFR continue their long-standing, trusting cooperation with the new project in Mississippi.
People from left to right:
Hirohito Imakoji, Managing Director, Liebherr Logistics USA, Co.
Joerg Ströbele, Managing Director, Liebherr-Logistics GmbH
Andreas Oy, Head of Business Development LS Region Central Europe, SSI SCHAEFER
Mauro Lunardelli, Head of Business Unit Logistics Solutions, SSI SCHAEFER
Kilian Ribhegge, Operations and logistics manager, Liebherr-Logistics GmbH
Peter Edelmann, CEO of SSI SCHAEFER Group
Robert Ebenhoch, CEO, Liebherr-Purchasing Services GmbH
Martin Barth, Managing Director, Liebherr-Logistics GmbH
Sebastian Goetz, Team Lead Logistics Engineering, Liebherr-Logistics GmbH